Invest in a decent CNC machine,it can use to start creating personalized items. Its not easy for people choose a good balance been affordability and reliability. Any recommendations we should look at? Which specs are most important?
Choose a suit size router for small woodshop
6090 model cnc router which working size is 600*900mm,its roughly 2*3ft size ,according to client feedback ,this size is mostly popular size .
2*3ft 6090 mini cnc router
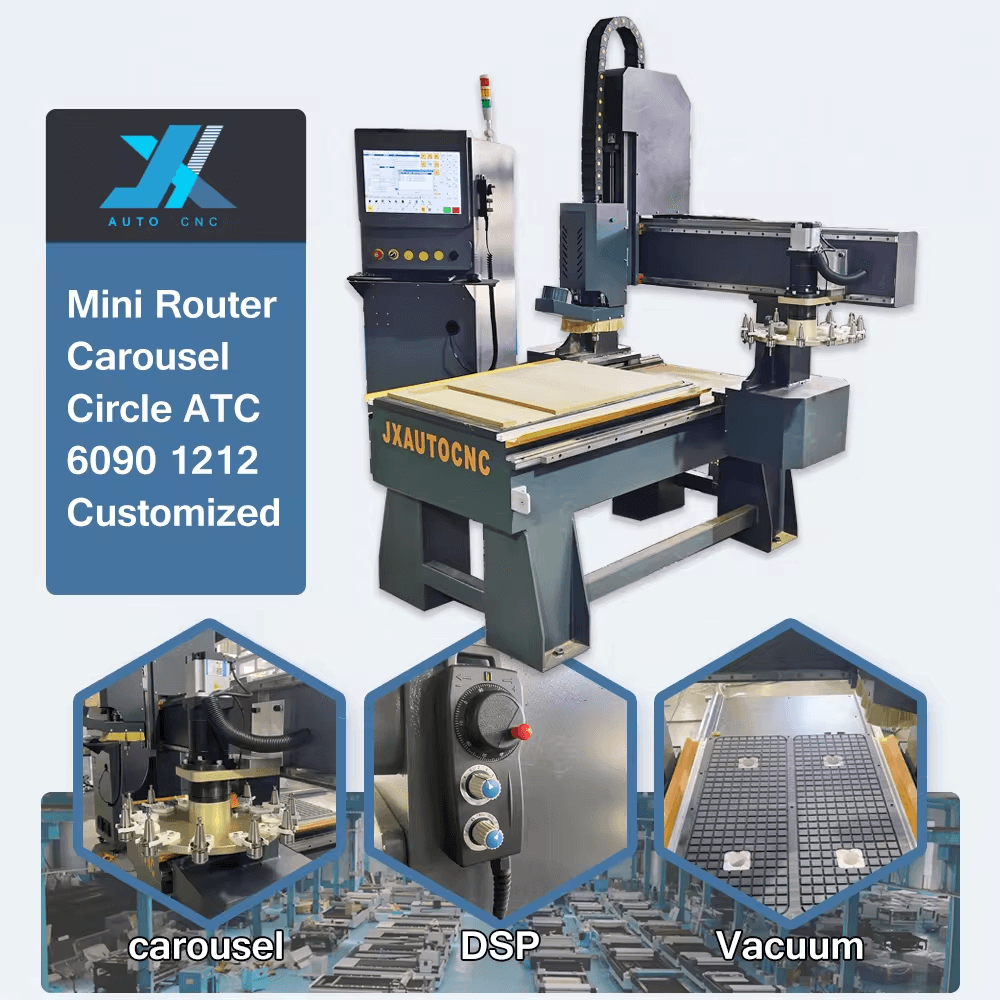
1.4*1.4ft 4040 400*400mm Mini Router,is also popular sale .
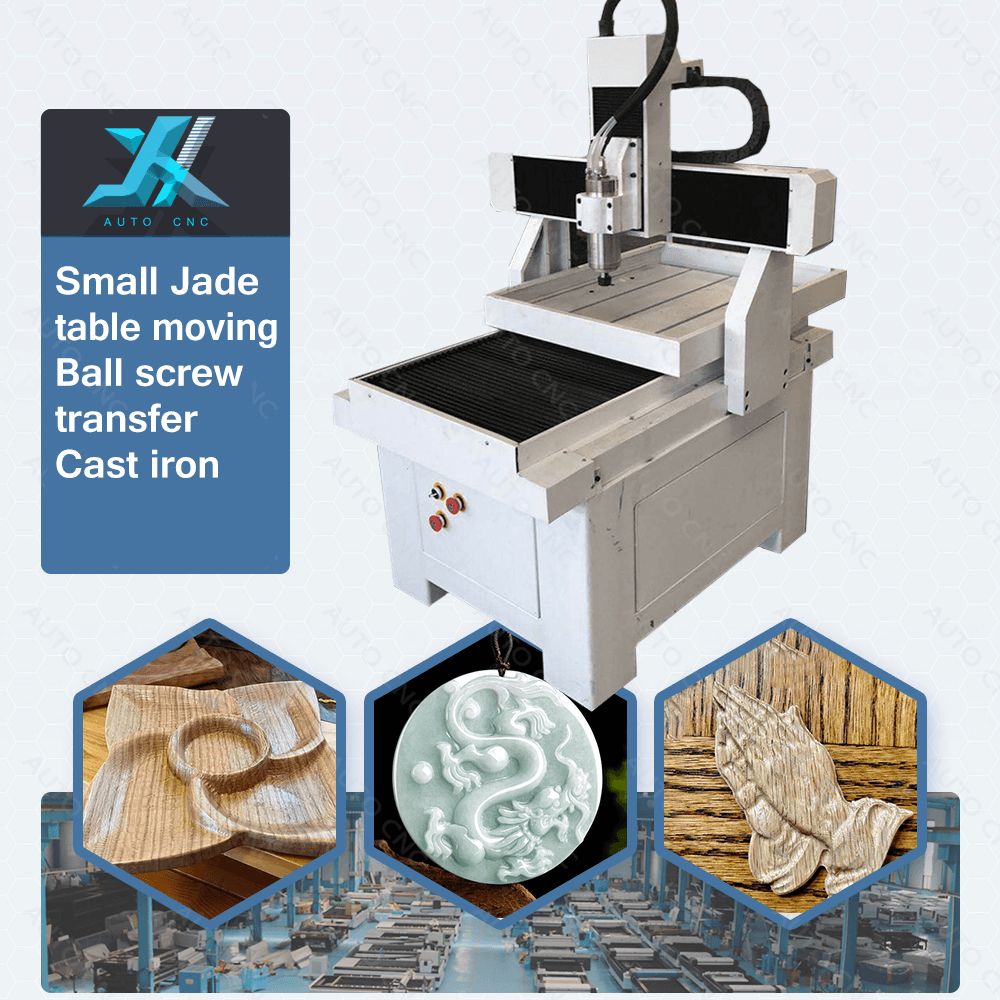
Except the XY working size ,there is a important consider its the Z axis height .
The Z-axis (vertical) travel capability of a CNC machine determines the maximum thickness of material that can be effectively processed. This limitation is crucial in considering the range of applications and materials you intend to work with.
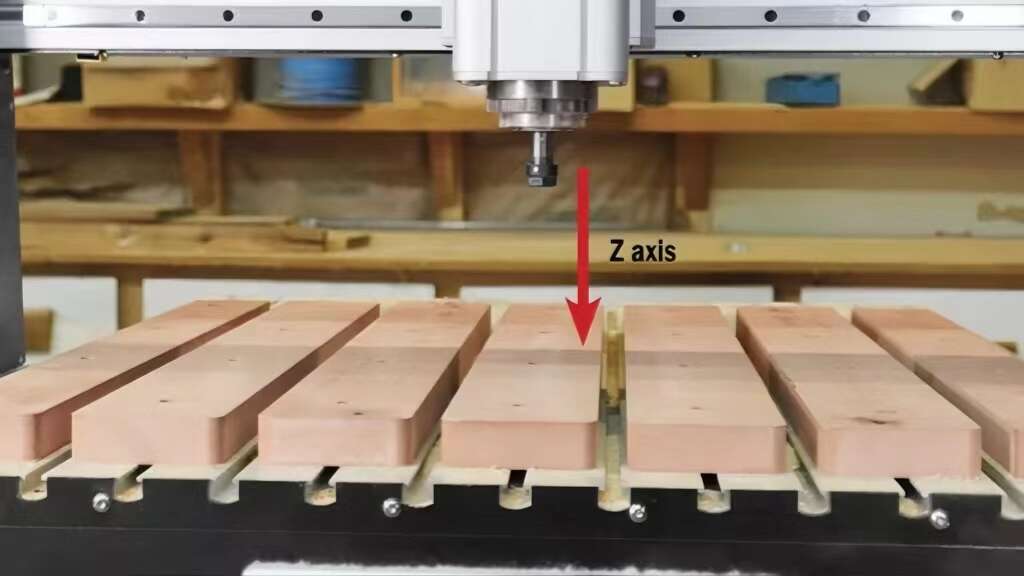
Three consider tips for Integrating a Mini CNC router into Your Workshop
As you embark on the journey of adding a Mini CNC router to your workshop, it’s essential to assess how well your workspace can accommodate this innovative addition.
Power Demands:
Mini CNC routers are typically pre-wired for either 110 or 220 volts, with varying amperage needs. It’s crucial to ensure that your power supply can meet or exceed the machine’s requirements.
Support Structures:
Some manufacturers provide stands for their CNC routers, but if not, you can customize a stand or bench to suit your needs. Having a bench or stand on casters gives you the flexibility to move the machine aside when not in use.
Dust Management:dust collector
CNC router generates a significant amount of fine dust, necessitating the use of a dust shroud around the cutting bit. This shroud allows you to connect it to a vacuum or dust collector. Operating a CNC without dust collection is not recommended. A large shop vacuum is sufficient for most mini cnc router units, but the dust can quickly clog the filter, reducing its efficiency. A dust collector with higher airflow (CFM) is often a better choice. You might receive a dust shroud with the machine; if not, they are typically available as accessories. Like other tools in your workshop, these shrouds typically accept 2-1⁄2″ or 4″ hose connections.
How to choose a suit controller system for mini cnc router ?
The Core of the Operation
After designing your project and mapping out the toolpath, this information must be transmitted to the mini cnc router. This can be achieved through a handheld pendant (commonly referred to as a fob) or by directly connecting a computer to the machine.
Some mini cnc router necessitate an external computer to be physically plugged in to execute the toolpath, requiring it to be stationed in the workshop alongside the machine. The mini cnc router typically interfaces with the computer via a USB port. To safeguard the computer from the dusty workshop environment, many users construct a protective cabinet. For instance, you can continue with other computer tasks while it’s executing the toolpath, which offers greater flexibility. With certain mini cnc router models, however, the computer becomes “locked up” during the cutting process, limiting its usage to mini cnc router operations only. Given that mini cnc router operation doesn’t require a high-end computer, if you opt for this setup, it’s advisable to purchase a cost-effective new or used computer dedicated solely to this task.
On the other hand, are designed specifically to operate in dusty environments without the need for a direct computer connection. When using a fob, you’ll design and plan your toolpath on a computer, save it to a flash drive, and then plug that flash drive into the fob. Irrespective of whether you use a direct computer connection or a fob, the functionality remains largely similar. You’ll utilize this device to calibrate your axes, regulate travel speed, and configure the machine.
Establishing Contact with the Bit
To ensure precise cutting, it’s crucial to calibrate the bit’s height relative to the workpiece. This process, known as “zeroing the Z axis,” involves lowering the bit until it makes contact with a touch plate and then resetting the Z-axis zero point on the fob (as shown in the accompanying photo). When ever you install a new bit or work with a different workpiece thickness, it’s essential to repeat this process to ensure accurate cutting. The touch plate may be included with the machine or purchased as an accessory, and its importance in achieving precise cuts can not be overstated.
So the DSP type controller is more popular in the mini cnc router .
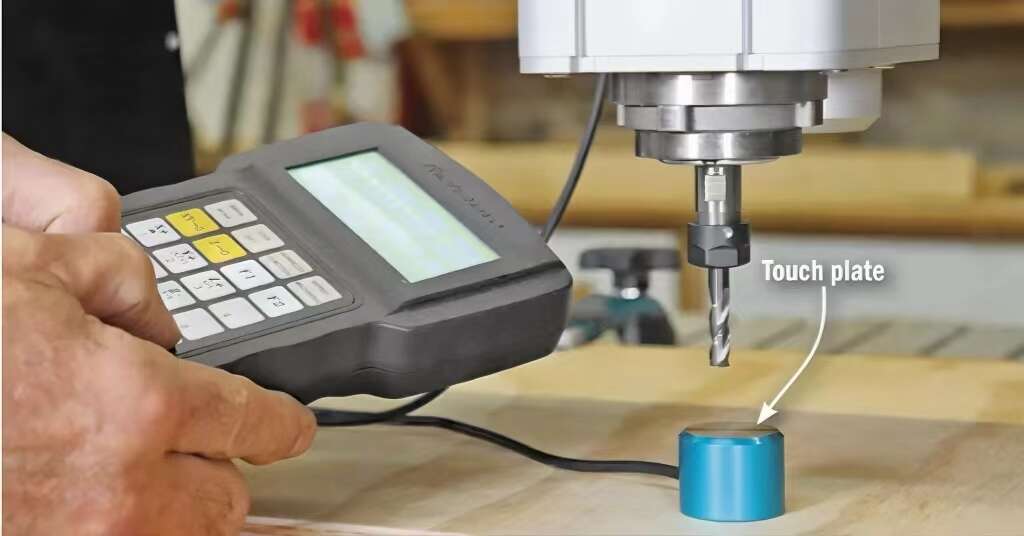